当将陶瓷坯体加热到它的熔点附近(熔点的0.6-0.9倍)时,便具有相当好的塑性。这是因为在高温下质点的热动能极大,结合能减少,因而外加机械力可以使晶面从一个平衡位置滑移到另一个平衡位置,形成离子品体的晶面滑移式塑性变形。由于这一特性,陶瓷也能像金属那样利用一系列的热加工工艺,如热锻、热拉、热轧等,以及热加工后的退火热处理,因此陶瓷不仅具有高密度、高机械强度,而在热加工处理后,使常态陶瓷中随机取向的晶粒,在一定程度上择优排列和定向再结晶,形成具有定向结构的陶瓷。这种陶瓷与单晶相似,具有宏观的各向异性。
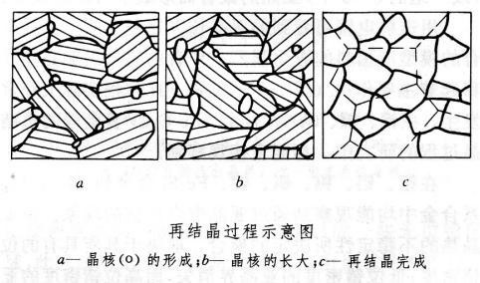
退火再结晶示意图
一、热锻
在金属再结晶温度以上进行的锻造工艺称为热锻。热煅又称热模锻,锻造时变形金属流动剧烈,锻件与模具接触时间较长。因此要求模具材料具有高的热稳定性、高温强度和硬度、冲击韧性、耐热疲劳性和耐磨性且便于加工。较轻工作负荷的热锻模可用低合金钢来制造。
金属毛坯锻前加热的目的是提高金属塑性、降低变形抗力、使之易于流动成形并获得良好的锻后组织。故锻前加热对提高锻造生产率,保证锻件质量以及节约能源消耗等都有直接影响。按所采用的热源不同,金属毛坯的加热方法可分为火焰加热与电加热两大类。
二、热轧
热轧是相对于冷轧而言的,冷轧是在再结晶温度以下进行的轧制,而热轧就是在再结晶温度以上进行的轧制。简单来说,一块钢坯在加热后经过几道轧制,再切边,矫正成为钢板,这种叫热轧。能显著降低能耗,降低成本。热轧时金属塑性高,变形抗力低,大大减少了金属变形的能量消耗。热轧能改善金属及合金的加工工艺性能,即将铸造状态的粗大晶粒破碎,显着裂纹愈合,减少或消除铸造缺陷,将铸态组织转变为变形组织,提高合金的加工性能。
热轧的特点:
1、能耗低,塑性加工良好,变形抗力低,加工硬化不明显,易进行轧制,减少了金属变形所需的能耗。
2、热轧通常采用大铸锭、大压下量轧制,生产节奏快,产量大,这样为规模化大生产创造了条件。
3、通过热轧将铸态组织转变为加工组织,通过组织的转变使材料的塑性大幅度的提高。
4、轧制方式的特性决定了轧后板材性能存在着各向异性,一是材料的纵向、横向和高向有着明显的性能差异,二是存在着变形织构和再结晶织构,在冲制性能上存在着明显的方向性。
三、急冷和缓冷
急冷也称淬火,是陶瓷坯体经高温保温烧结后,将坯体急速降温的一种热处理工艺。急冷的主要作用如下:
①保留高温相组成,避免缓冷过程中的分凝、析晶和相变,以满足某些应用对材料的性能要求;
②产生表面压应力,以提高坯体的抗张强度。
例如,独石电容器常采用急冷工艺,以保特其高温态的晶体结构,防止玻璃相析晶,因而可使瓷体致密,减小介质损耗,提高绝缘电阻。急冷可采用油冷、风冷等方法。缓冷也称退火。陶瓷坯体经高温烧结后,在炉中缓慢冷却,或在某个温度下进行长时间保温。缓冷的作用主要有以下两点。
①促使坯体在冷却过程中晶体长大、分凝、析晶和相变,以满足某些应用对材料性能的要求。如晶界层电容器采用缓冷工艺,可使晶粒晶界层变厚、绝缘电阻增高、抗电强度提高。
②消除坯体表面和内部应力,使相平衡过程充分进行。陶瓷是一个多晶和多相系统,不同物相之问的膨胀系数、相同物相不同晶轴之间的膨胀系数常常大小不同,因而在烧成后的冷却过程中相邻部分的收缩率也往往不同,这将带来晶粒晶界或相界两侧的应力差。膨胀系数大的将承受张应力,膨账系数小的承受压应力。如果这种应力足够大时,将在界面附近出现裂纹。晶粒越粗大,这种应力积累越大,出现裂纹的可能性也越大。降温速度过快,这种应力来不及传递和缓沖,则更容易出现裂纹。这种应力的存在和裂纹的产生,对坯体强度非常有害,对该种情况常常采用缓冷措施,以消除内应力。
粉体圈 整理
了解优质装备供应商,请联系客服18666974612(微信同号)