随着工业应用要求的不断提高,均质材料的局限性逐步显现,无法满足严苛的服役环境对同一零部件的不同部位提出的不同性能要求,比如超音速燃烧冲压式发动机等的燃烧室壁需要耐高温耐腐蚀来抵御高温燃烧气体的侵蚀,而另一侧与液氢接触,需要承受极低的温度。于是,人们开始思考将两种不同的材料联合使用。然而,不同材料的界面热力学特性匹配不好,仅经简单的结合在极大的热应力下还是会遭到破坏。为了解决这一问题,日本科学家平井敏雄提出了梯度功能材料(FGMs)的概念。
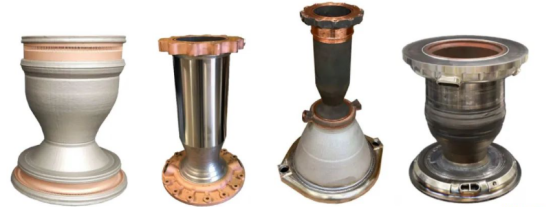
美国航空航天局(NASA)制备的多金属梯度材料组件
梯度功能材料(FGMs)是一种由两种或多种材料复合而成的新型非均质复合材料,通过连续地改变两种材料的组成和结构,FDMs可以设置一个膨胀系数缓和区以降低热应力,使材料间的内部界面消失,从而得到功能随组成和结构的变化而渐变的非均质材料,实现零部件内各位置的材料与性能综合优化,为解决复杂应用环境下材料性能不匹配的问题提供了一种创新的解决途径。
目前,FDMs材料可分为梯度功能薄膜/涂层以及梯度功能构件。
梯度功能薄膜
梯度薄膜是一种涂覆型梯度材料,具有均质薄膜无法比拟的优越性,它允许根据实际使用需求来定制材料的成分和梯度,通过充分利用梯度层或过渡层可有效缓解硬质涂层与软基体(如Al、Mg合金)相容性差的问题,因此在表面处理技术中得到了广泛的应用。梯度薄膜的制备方法主要有气相沉积法和喷涂法两种。
1、气相沉积法
气相沉积技术是利用气体在物体表面沉积形成微米级、亚微米级薄膜或涂层的一种技术,一般用于提高基体耐磨损、耐腐蚀或热性能,常用的方法包括化学气相沉积和物理气相沉积。
(1)化学气相沉积(CVD)
化学气相沉积法是把含有构成薄膜元素的气态反应剂或液态反应剂的蒸气及反应所需其他气体引入反应室,在衬底表面发生化学反应,并把固体产物沉积到表面生成薄膜的过程。通过调节原料气流量和压力等,CVD法可精确控制材料的组成、结构与形态从一种组分到另一种组分连续变化,从而制备出特定功能的梯度功能材料。CVD法适用于复杂形状的材料进行表面沉积,可轻松实现分散相浓度的连续变化,沉积表面光滑致密,但制备时大都处于高温高压环境之下,大尺寸基材表面进行沉积时易变形。
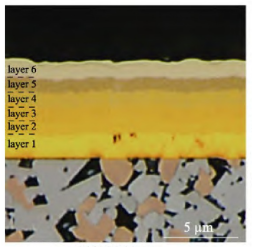
化学气相沉积制备的Ti N-Ti B2梯度材料
(2)物理气象沉积法
物理气相沉积是利用蒸发或溅射等物理形式,将金属、合金、化合物等无机材料气化成气态原子、分子或部分电离成离子,并通过低压气体(或等离子体)过程,在基体表面沉积具有某种特殊功能薄膜的技术。相比CVD法,PVD法的沉积温度低,对基体热影响小;但沉积速度较慢,且不能连续控制成分分布,所制得的材料致密性较差,而且涂层结合力较低,涂层易于剥落。
2、热喷涂法
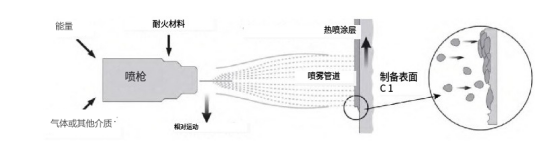
热喷涂原理
热喷涂技术可利用不同的热源和喷涂设备(如等离子弧、电弧以及火焰等)将喷涂材料加热成熔融或半熔融状态,再使用高压气流将其雾化,并以一定的速度喷射沉积到经过预处理的基体表面从而形成具有特定功能的涂层。热喷涂法的喷涂原料范围广,涵盖金属、合金、陶瓷、金属-陶瓷、高分子材料等,在制备梯度功能涂层时,通过调整各种喷涂材料的比例,可轻松实现涂层中成分和性质的渐变,具有沉积效率高、涂层不受零件基材状态和大小限制的优点,但得到的梯度功能材料孔隙率高,层间结合力低,涂层较容易剥落。
梯度功能构件
梯度功能构件是在构件内部或表面具有逐渐变化性能的材料组合,可在整个三维结构中实现性能的渐变,如在医疗器械领域,具有梯度功能的人工骨骼植入物可在不同位置具有适当的弹性模量,模拟出天然骨骼的性能。在航空航天领域,通过梯度设计,可以在构件内实现性能的逐渐变化,满足不同位置所需的强度、耐磨性、耐热性的要求。因此,梯度功能构件的制备与二维的梯度薄膜制备不同,需要在构件内部或表面实现材料性质的渐变。目前主要有激光增材制造、粉末冶金法、离心铸造法和高温自蔓延技术等
1、激光增材制造
激光增材制造是指以高能密度激光束为热源,逐层熔化粉末材料以形成目标零件的过程,具有一次成形、无模成型、低成本和高效率等特点,能够实现复杂形状、多层结构件的快速制造。由于激光的能量密度高,热影响区小,采用激光作为热源进行增材制造能够更好地保证所制备零部件的致密度以及尺寸精度。同时激光能够熔化一些难熔材料,例如金属/陶瓷等,所以该技术的材料成形范围广泛。
在梯度功能材料的制备上,激光增材制造可通过改变熔化粉末的组分配比,实现材料成分和性质的改变。目前,激光增材制造技术主要分为选区激光熔融/烧结技术(SLM/SLS)以及直接激光沉积技术(DLD)。
(1)SLM/SLS技术是将一层粉末材料平铺在已成型零件的表面上,激光束按照该层的截面轮廓在粉层上扫描,使粉末的温度升到熔化点,使之与下面已成型的部分实现粘结、烧结,如此逐层烧结,直至完成整个模型,由于激光光斑尺寸小,成形的样件精度很高,但层层铺设的粉末供给方式,导致梯度大多只能在垂直于铺粉层的方向上变化,在其他方向上变化非常困难,因此SLM/SLS技术在成形梯度材料方面较为复杂。另外由于受设备尺寸限制,难以自由成形大尺寸构件。
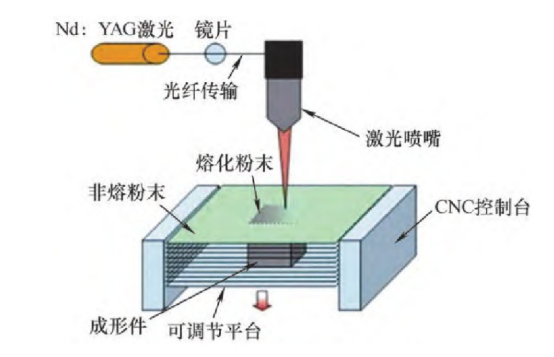
(2)DLD技术是将粉末或金属丝形式的原料输送到同时聚焦激光束的基板上,从而形成一个小熔池并逐层连续沉积材料,由于可以任意对不同材料进行混合,极大地拓展了材料的设计自由,不受构件尺寸限制,适合复合材料/功能梯度材料的制备。
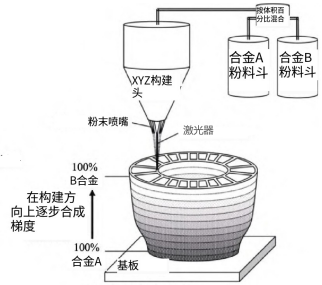
DLD技术原理
2、粉末冶金法
粉末冶金法制备功能梯度材料是指先将原料粉末按不同比例均匀混合, 然后以梯度分布方式逐层堆积排列, 再压制烧结而成为功能梯度材料的过程,常用的烧结方式有热等静压、冷等静压+无压烧结、放电等离子烧结、热压烧结等。利用粉末冶金法,可通过选用不同的原材料粉末按设计好的梯度进行排列,即可制备出满足需求的梯度材料。由于粉末冶金法操作简单,成本也相对较低,适于工业化生产且可制备大尺寸的梯度功能材料,但因烧结体颗粒组成、内部结构及烧结环境存在非均匀性, 在烧结过程中样品易出现非均匀收缩现象,故需要进一步研究如何控制保温时间、保温温度、冷却速率等参数以制备形状复杂、低孔隙率的功能梯度材料。
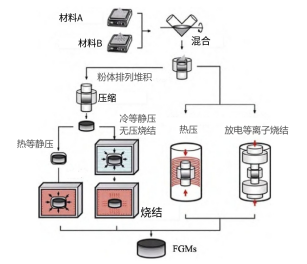
粉末冶金法制备梯度材料
3、离心铸造法
离心铸造是利用强化相质点与液态金属熔体之间的密度差异,将液态金属搅入旋转铸型中,通过控制旋转工艺参数,实现颗粒在样件内沿离心力方向分布,制备出强化相呈梯度分布的功能材料。离心铸造法的优点在于设备简单,铸造成本低,可实现高致密度、大尺寸梯度功能材料的批量生产,但因需采用熔融态金属为原料,故无法制备高熔点的陶瓷系梯度材料,同时由于这种方式是基于组分密度差异的原理,故组分间必须存在密度差,且所制备的梯度材料因离心力作用,一般只能制备环形或管状部件。
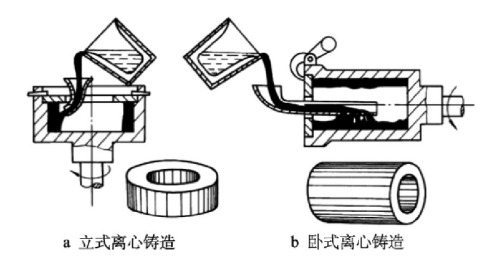
立式(左)及卧式(右)离心铸造机结构
离心铸造梯度材料截面SEM图
4、自蔓延高温合成法
自蔓延高温合成法(SHS)是一种是利用外部提供的能量诱发反应物之间高的化学反应热,通过物料的自加热和自传导作用,使反应自动向尚未反应的区域传播,直至蔓延至整个试样,从而制备出所需合成材料的技术。
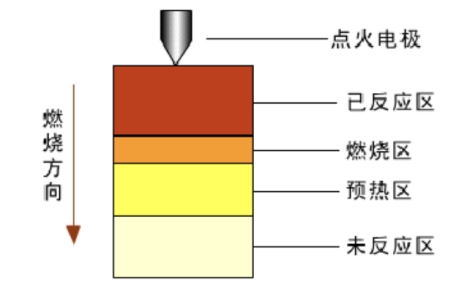
利用SHS制备梯度材料时,首先将具有可燃性的金属元素粉末与非金属粉末按照预设的梯度层叠铺设后加压成型为坯样,然后通过提供少量的外部能量诱发整个坯样发生自蔓延反应,在瞬间产生数千度的高温环境,从而制备出高温合成的梯度材料,不仅能耗极低,加工时间也很短,同时合成过程中的自纯化效应,即低熔点的杂质可逸出体系,能够提高产物的纯度,但不同组分材料发热量有差异,导致自蔓延过程难以控制,而且因为需利用反应物的自放热,故只适于生成热较大的化合物合成,这使得梯度材料的原料选择非常有限。
小结
梯度功能材料能满足复杂工作条件下,同一件材料不同部位具有不同的性质或功能的要求,根据结构和应用领域的不同,梯度功能材料可进一步分为梯度功能薄膜和梯度功能构件,梯度功能薄膜主要应用于软基体的表面处理,可用气相沉积法和热喷涂法制备。而梯度功能构件则可在整个三维结构中实现性能的渐变,应用范围更广,目前已成功制备出具梯度功能的生物仿生材料、航空航天材料等。未来,探索不同成分空间内的最优过渡路径,实现材料组织及元素的平滑过渡将使梯度功能材料制备的主要研究方向。
参考文献:
1、宋晨晨,严新锐,张子傲等.功能梯度材料制备技术研究进展[J].表面技术.
2、张坚,张官兵,赵龙志等.梯度功能材料制备技术的现状与展望[J].热加工工艺.
3、宋学平,黄健康,樊丁.增材制造技术制备金属梯度功能材料的研究进展及展望[J].金属加工(热加工).
4、杜东方,张明,余盈燕等.增材制造高性能功能梯度材料研究进展[J].锻压装备与制造技术.
粉体圈Corange整理
本文为粉体圈原创作品,未经许可,不得转载,也不得歪曲、篡改或复制本文内容,否则本公司将依法追究法律责任。